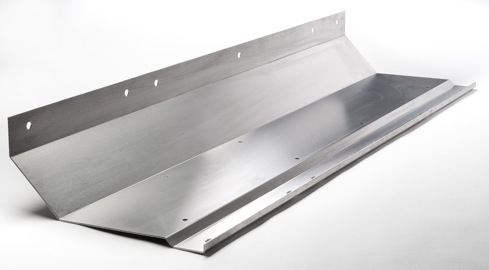
High-Volume, Large HVACR Sheet Metal Fabrication Project
High-Volume, Large HVACR Sheet Metal Fabrication Project
When a long-standing Ajax HVACR customer modified a large component to improve their product performance, they came to Ajax for help with sheet metal fabrication. A critical link in a very long supply chain for an expensive and complex product, the 43-inch precision part includes five compound bends.
Sheet Metal Fabrication Project Specifications:
- Product Name: HVACR Header Plate
- Project Scope: Manufacture 43-inch long part that includes five compound bends
- Product Description: Mass volume header plate for commercial/industrial heating/cooling unit
- Capabilities and Processes: Turret Press Blanking; Compound Forming; Prototyping; PPAP; SVPP; Custom Kit Packaging
- Tightest Tolerance: .003 inch hole diameter; one degree of forming
- Material Thickness .080
- Material Used: 5052 H32 Aluminum
- Volume: 20,000 parts annually
- Lead Time: KANBAN
- Delivery Location: Offshore
- Standards Met: RoHS; REACH
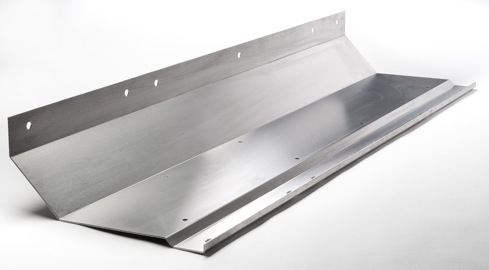
A 43-inch precision HVACR part that includes five compound bends.
Let's Get Your Project Underway!
Ajax sales engineers can help you determine the most cost-effective solution for your stamping and sheet metal fabrication project.