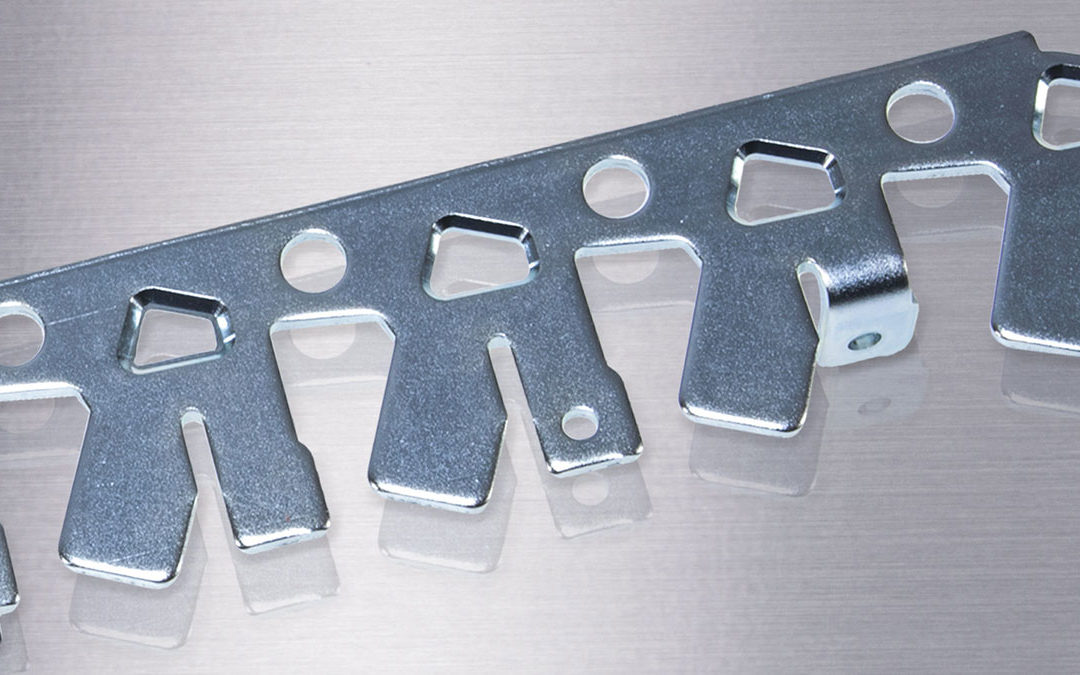
Time For Metal Forming To Shine
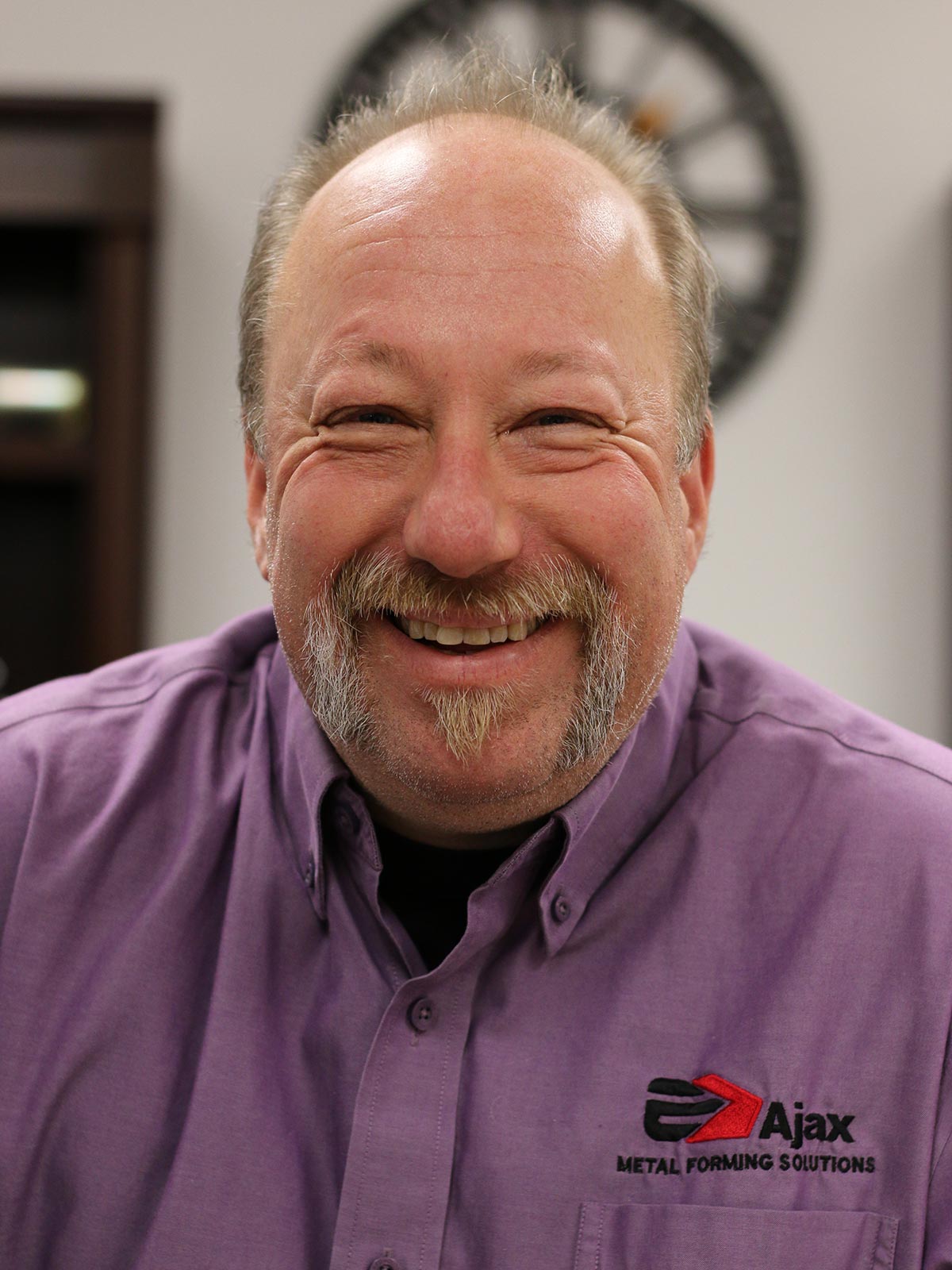
A Message Of Inspiration From Ajax President Kent Djubek.
America has a remarkable ability to land on its feet. That will once again be the case as we fight past this current pandemic.
The management group here at Ajax remains very confident in our ability to emerge from this crisis stronger, smarter, and better prepared. Our 75 arduous but productive years have hardened us against challenges. We know we can win.
Three years ago, we teamed up with Heartland Equity Partners, a community-minded investment fund with an outstanding record of stewardship. We’re fortunate to have a leadership team this experienced and resourceful.
On the people side of the equation, there’s even more to appreciate. Our department heads are proven individuals who are committed to their assignments. Our colleagues on the plant floor are demonstrating impressive bravery as they press on despite uncertainty.
We also view this moment as a rare opportunity to form our young people into the manufacturing leaders of the future. They’ll fall back on this experience and use it to project confidence each time a storm gathers on the horizon. They’ll also learn critical steps for maintaining the wellness of a workforce as they witness everything we’re doing at both our locations to prevent spread.
Most importantly, our essential industry customers continue to demand the parts and services Ajax provides. With guidance from the National Association of Manufacturers, the Centers for Disease Control, the Precision Metalforming Association, and the U.S. Chamber of Commerce, we have followed guidelines perfectly and have maintained our critical supplier status.
Due to the nature of COVID-19, air handling and purification is an area of immediate need among health care providers. With decades of experience serving heating, ventilation, air conditioning, and refrigeration companies, as well as medical instrument manufacturers, Ajax will continue to provide our customers with the formed parts they require to meet this demand. Ajax is indeed part of the solution.
My belief that America has the resources and the will to endure is shared by many. Congress is taking action to pump new life into the American economy. Our manufacturing community has the perseverance to get past this character-building moment.
It’s time for the metal forming industry to shine. All it will take is teamwork.