Minneapolis, March 30, 2020 – When it comes to COVID-19 illness, ventilators can save lives. But there’s too few to go around.
That’s why University of Minnesota Anesthesiologist Stephen Richardson came up with a ventilator design that uses low-cost, off-the-shelf parts and could be manufactured quickly. But he needed a prototype for his design, so he turned to the U of M’s Earl E. Bakken Medical Devices Center (BMDC) for assistance.
The BMDC team, headed by Dr. Art Erdman, a long-time University of Minnesota mechanical engineering professor, set up an emergency manufacturing and assembly facility and is now on generation 3.2 of the ventilator prototype, now called the “Coventor.”
“To date, we have been addressing at least five projects in response to the crisis. The first is the Coventor-A COVID-19 Ventilation System,” Dr. Erdman stated Friday in a BMDC email. “We are in awe of the tremendous outpouring of all the offers to help us in our development of a low-cost ventilation system in response to the COVID-19 crisis.”
Cara Piazza, a U of M Graduate Student in Mechanical Engineering who works on the Coventor project at the BMDC, said Dr. Richardson presented his idea a few weeks ago. “We were all hands on deck with this project. It’s a great idea. We do what we do for moments like this.”
The coronavirus pandemic has resulted in a global shortage of ventilators, devices that are critical to the survival of many COVID-19 patients. Many ventilators were already in use by non-COVID-19 patients, leaving emergency rooms in desperation.
“What’s unique about our design is that it’s a low-cost, mass-production unit that gets the job done. It’s designed for emergency use. We can send our design all over the world, and it can be reproduced.”
Cara is responsible for working with companies who are partnering with the BMDC to design and develop parts that are not available off-the-shelf or online. More than 300 companies and individuals submitted offers to help, she said.
Making The Connection
“There were key components of our generation 3.2 design that needed sheet metal. Through our connection with Ajax, we were able to meet a need for 25 units,” Cara said. “We may have units in hospitals next month, maybe even sooner.”
The connection happened almost by chance. A member of the Ajax board picked up the Sunday paper and read about the BMDC project last week and realized that Ajax was in a good position to assist.
Ajax manufactures parts for HVACR (heating, ventilation, air conditioning and refrigeration), healthcare, transportation, agriculture, and other critical industries. The company is classified as an essential service provider by the U.S. Department of Homeland Security and remains open.
The board member, through a mutual friend, facilitated introductions Sunday morning. Dr. Richardson explained his idea to the Ajax team and sent a drawing for examination. Kent Djubek, Ajax president, set the wheels in motion that day.
Into Production
By Sunday afternoon, Kent had enlisted the services of Talon Ganz, engineer and lead programmer at Ajax, to apply his expertise in SolidWorks® CAD/CAM applications. Talon quickly prepared the files needed to operate Ajax’s computerized fabrication machinery.
Talon and Kent recommended several design improvements that would lower costs and speed production. Rather than machining parts from billet aluminum, which would have been slow and expensive, the Ajax team decided to laser-cut the parts from stainless steel, a durable material that is widely available. The Ajax team also suggested the elimination of through-bolts by using the Ajax auto tapper.
The plan worked out. The stainless blanks were cut on one of the Ajax Salvagnini L3 fiber optic lasers, then deburred and formed on a press brake. By Monday afternoon, the team had ten units for Cara to examine. She then contacted Kent with a few more improvements, and by late morning on Wednesday, just three days after the drawings were delivered, Cara picked up 25 assembled enclosures that she rushed back to the BMDC for final assembly. “We had super-fast sheet metal work,” she said.
Ajax provided all programming and consulting services, materials, and labor for this project at no cost to the BMDC. The company keeps stainless steel on hand, so the team did not have to wait for materials.
“What was most gratifying to me was the enthusiasm our colleagues had for this project,” Kent said. “We prioritized this work because we knew the need was extreme. Community service has an empowering effect on people.”
About The University of Minnesota Earl E. Bakken Medical Devices Center
The BMDC, located in Minneapolis, Minnesota, is missioned to train the next generation of medical device innovators, to accelerate medical device development, to support teaching programs, to interface with the medical industry, and to help improve health care worldwide.
The BMDC is the namesake of electrical engineer and mathematician Earl E. Bakken, a founder of Medtronic, one of the world’s largest medical device companies. Mr. Bakken developed the first external, battery-operated, transistorized, wearable artificial pacemaker in 1957.
About Ajax Metal Forming Solutions
Ajax Metal Forming Solutions is an ISO 9001:2015 metal forming solutions provider serving industrial and commercial manufacturers. The company’s diverse ownership group includes 3rd generation family members, key company leaders, and Heartland Equity Partners, a mission-based private equity company.
Ajax is celebrating its 75th year in 2020. The company employs about 65 colleagues at the company’s Minneapolis campus.
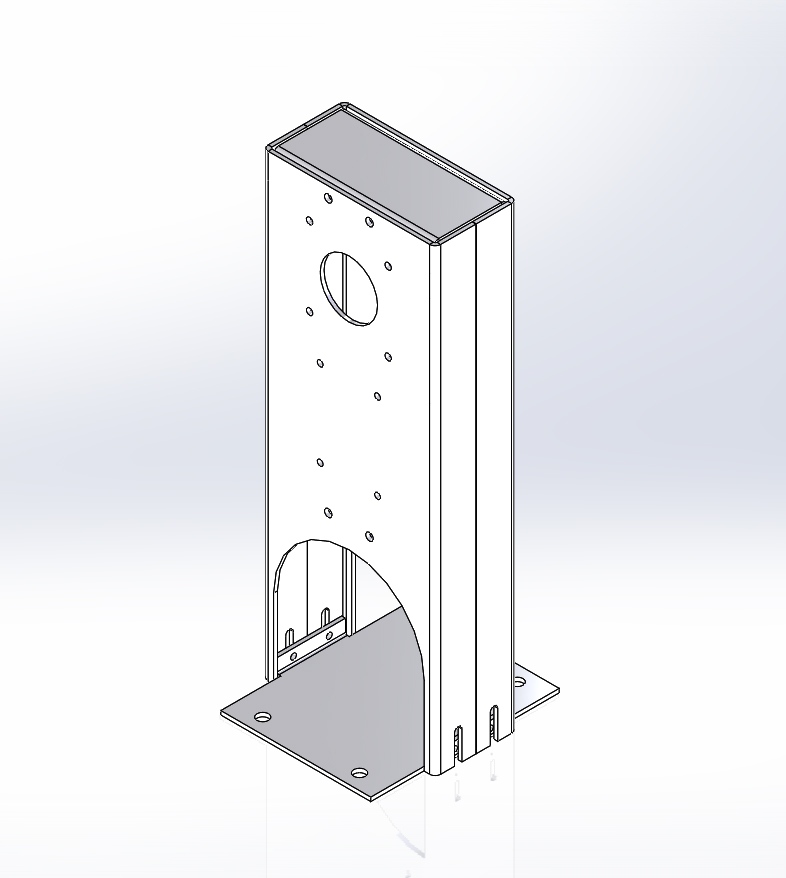
The Components Produced By Ajax – This is a SolidWorks® model of the 4-part Coventor enclosure produced by Ajax Metal Forming Solutions of Minneapolis, Minnesota. Ajax recommended several design improvements that made the Coventor faster and easier to manufacture and assemble.
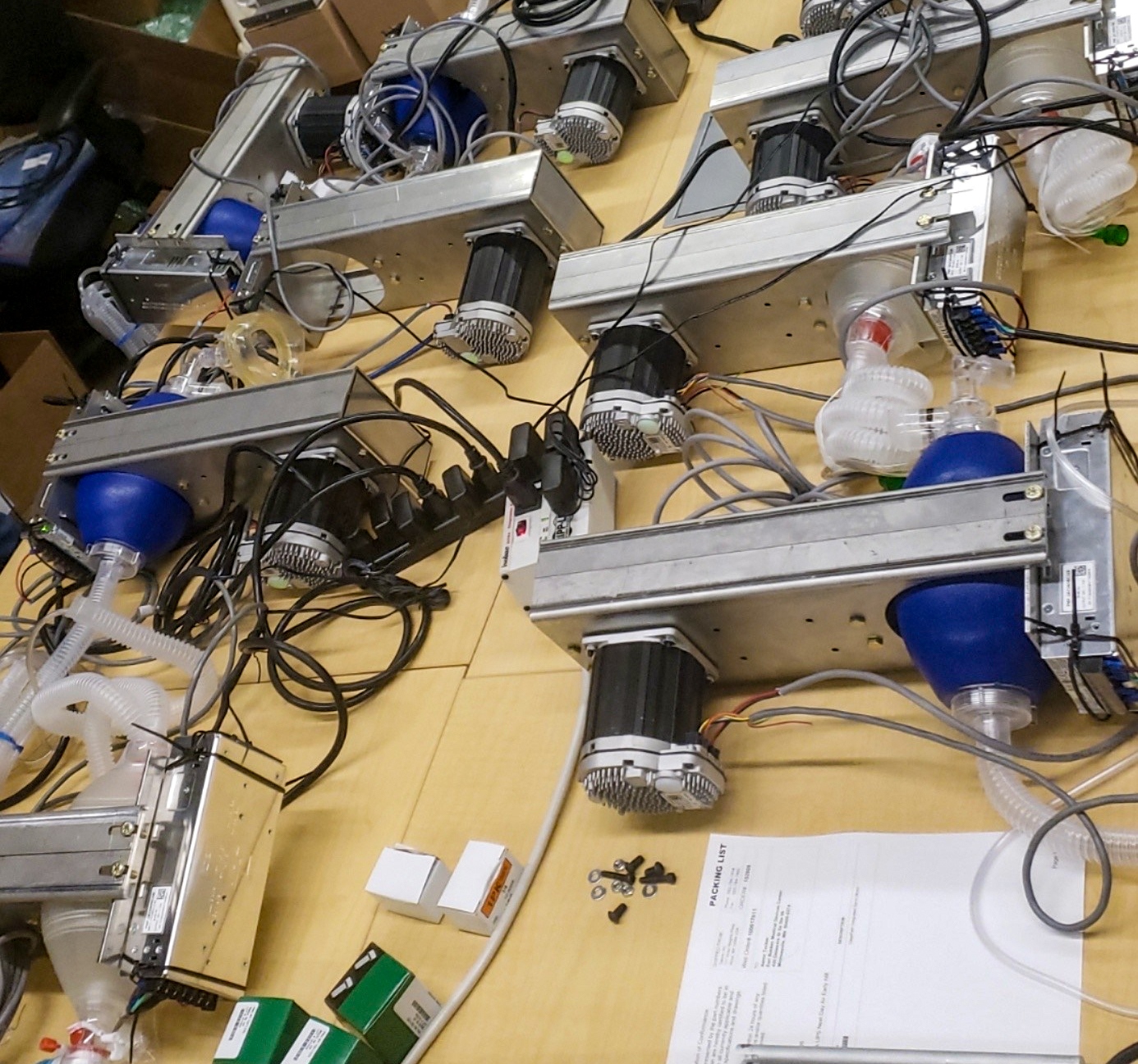
The Coventor Prototypes – Ajax delivered 25 assembled Coventor enclosures to the University of Minnesota Earl E. Bakken Medical Devices Center on Wednesday, March 25, 2020. The BMDC set up an emergency manufacturing facility to complete the Coventor assemblies.