Sheet Metal Fabrication
Excellence At Every Stage In The Process.
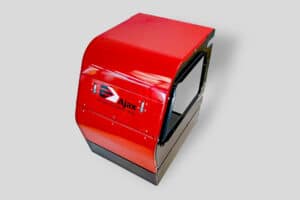
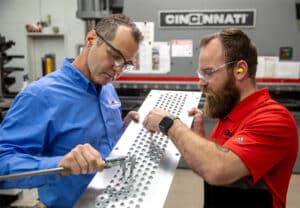
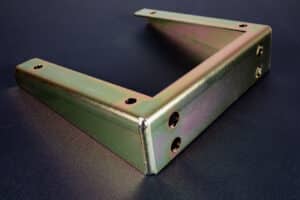
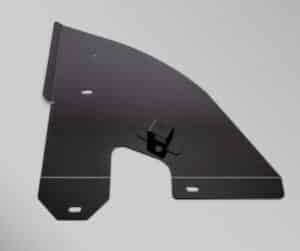
Fabrication Solutions From Prototype to Delivery.
Ajax Metal Forming Solutions is an award-winning manufacturer producing fabricated metal parts for OEMs and their suppliers in the climate control, transportation, architecture, power generation, medical, engineered products, and consumer goods industries. Our sheet metal fabrication services include fiber laser cutting, press brake forming, CNC turret punching, welding, finishing, assembly, kitting, and other metal forming services from our locations in Minneapolis, MN, Wilson, NC, and Tucson, AZ.
As metal forming professionals, we understand the value of long-term business relationships.
We’ve invested heavily in workforce training, new machinery, production software applications, and floor space. We have the means to fabricate your most difficult parts quickly, perfectly, and at a competitive price. For these and other reasons, many Ajax customers have been with us for decades.
Sheet Metal Fabrication FAQs
What Is Sheet Metal Fabrication?
Sheet metal fabrication is a manufacturing process that transforms flat sheets of metal into custom-designed parts used in a wide range of consumer, commercial, and industrial products. This process includes metal cutting using advanced fiber-optic lasers or traditional shearing, forming using precision press brakes, and punching on CNC turret presses. Ajax Metal Forming Solutions has specialized in high-quality sheet metal fabrication since 1945, now in our eighth decade of serving customers.
What Industries Require Sheet Metal Fabrication?
Ajax provides precision sheet metal fabrication to Original Equipment Manufacturers (OEMs) across diverse industries such as medical devices, household appliances, HVAC (air climate control), construction, electronics, transportation, and agriculture, among others. OEMs typically choose sheet metal fabrication for complex parts produced in small to medium volumes, requiring precision, consistency, and strict adherence to detailed specifications.
What Materials Does Ajax Use in Sheet Metal Fabrication?
Ajax fabricates a wide range of materials, including stainless steel, galvanized steel, mild steel, aluminum, copper, brass, bronze, and specialty materials like titanium. Selection criteria, including ductility, strength, corrosion resistance, weight, availability, and cost, are carefully considered to ensure optimal material choices for each application. Ajax’s team possesses extensive expertise gained through rigorous training and hands-on experience, enabling them to consistently match material properties to application requirements.
For instance, stainless steel is often recommended for applications that require strength, durability, aesthetic appeal, or hygiene, such as in medical devices. In contrast, aluminum is preferred for lightweight parts that require corrosion resistance or for components that need non-magnetic characteristics to minimize interference in electronic devices.
What Are Common Processes in Sheet Metal Fabrication?
Cutting is typically the first step in sheet metal fabrication. Modern fabrication primarily utilizes advanced fiber-optic laser cutting, which provides exceptional accuracy, minimal waste, and precise, burr-free edges. Ajax’s highly skilled programmers use advanced CAD/CAM software for laser cutting, significantly enhancing productivity and eliminating production bottlenecks. Traditional shearing remains a reliable method for simple straight cuts.
Another essential process involves CNC turret punch presses, which perform piercing and extrusion operations. These punch presses feature rotating turrets that allow rapid tool changes even during operation, significantly enhancing productivity and accuracy. Ajax invests heavily in employee training to ensure these sophisticated machines consistently deliver high-quality results.
Press brake forming is a critical fabrication step, bending sheet metal by clamping it between a punch and die and applying controlled force. Ajax employs advanced five-axis press brakes with touchscreen controls, precisely programmed to execute exact angles and dimensions. Press brake forming accommodates both simple and complex bends, handling various material types and thicknesses.
What Finishing Processes Are Available?
Following fabrication, Ajax offers comprehensive finishing services, including powder coating, anodizing, electro-polishing, and plating. Additionally, Ajax provides product assembly using specialized fastening hardware, robotic welding services, and kitting—packaging and shipping related parts together for efficient final assembly at our customers’ locations.
How Does Ajax Ensure Part Quality?
Quality assurance is central to Ajax’s sheet metal fabrication processes, ensuring every component meets stringent standards. Ajax employs diverse inspection methods, from handheld digital micrometers and calipers to advanced laser scanning technologies. These rigorous quality checks ensure dimensional accuracy, surface integrity, and material consistency, protecting against defects and maintaining Ajax’s reputation for excellence in fully compliant part deliveries.