Progressive Stamping
The Intersection of Efficiency and Quality.

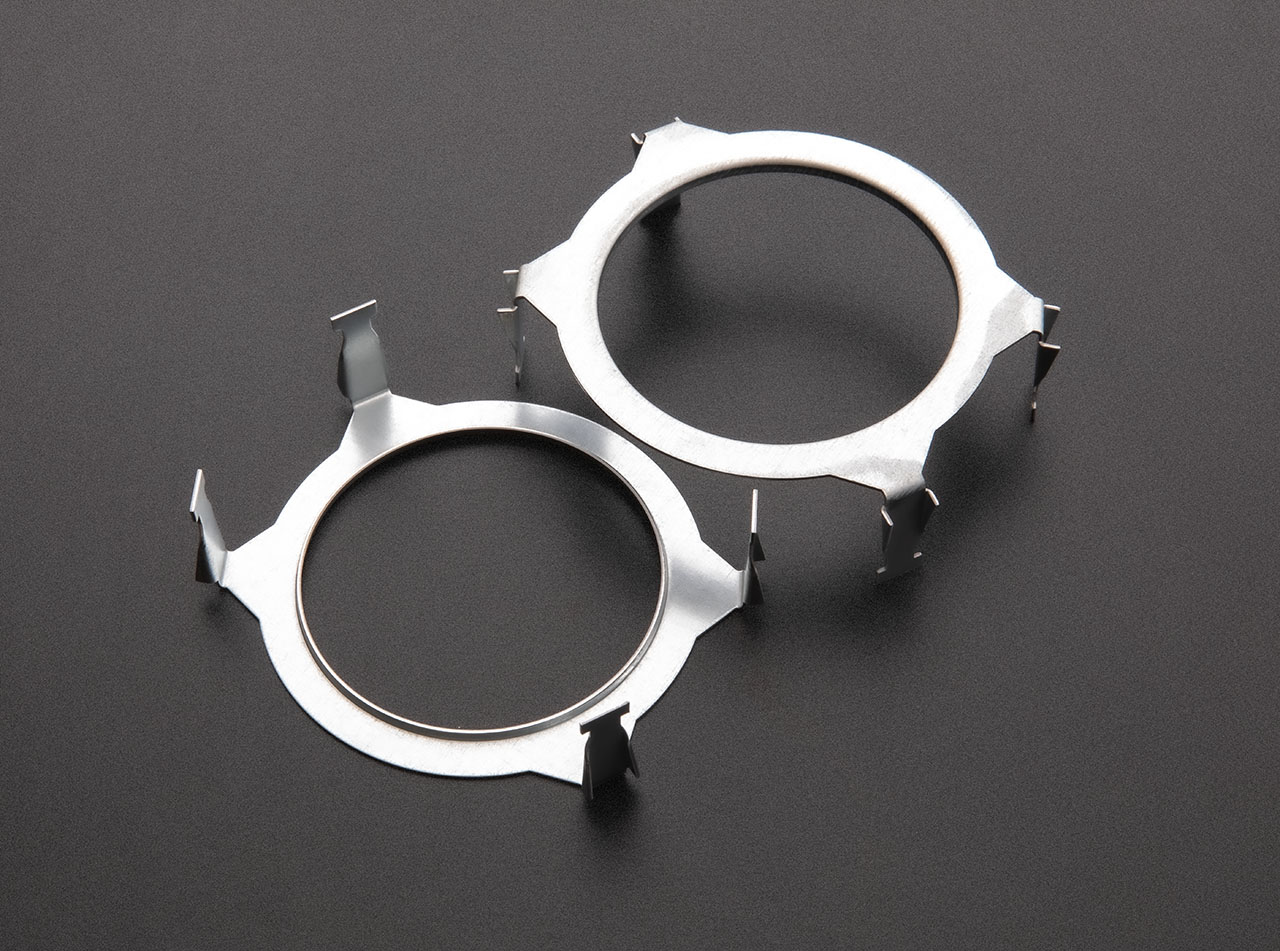
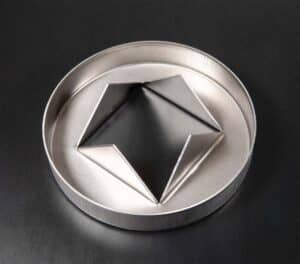
High-Volume Progressive Stamping Solutions
Precision. Speed. Efficiency.
Progressive stamping is the ideal solution for producing complex metal parts at scale. By feeding material continuously through a series of automated operations, this process ensures:
- Consistent, high-quality output
- Fast production rates
- Minimal material waste
Perfect for demanding, high-volume applications across industries like transporation, medical, electronics, and more.
Better Solutions, Better Results.
Ajax designs stamping solutions to meet or exceed our customers’ production goals, even those with tight tolerance requirements. Modern equipment enables more automation at each step in the process and keeps our operator safety record among the highest in the industry. Ajax sales engineers have vast experience designing stamping lines that produce parts reliably and keep our customers’ production lines humming.
Progressive stamping is ideal for long-run, high-volume parts, like these parts that require brass, bowl-fed hardware insertion.
Progressive Stamping FAQs
Why Choose Progressive Metal Stamping?
Progressive metal stamping employs sophisticated sets of dies to perform a series of stamping operations automatically and continuously. Unlike manual stamping, progressive stamping significantly enhances productivity, making it ideal for high-volume manufacturing. Metal strips enter the stamping press through a rotating feeder system that straightens (decoils) the material before it enters the die set. The feeder system may also apply vanishing oil to minimize die wear. A skilled press operator can produce thousands of uniform parts in a short period of time, reducing per-unit cost, minimizing non-compliance, and limiting material waste.
While highly efficient, progressive stamping presents unique challenges. High-quality die sets require significant upfront investment and meticulous design and maintenance to prevent production issues. At Ajax, our in-house tooling department addresses these challenges directly, eliminating reliance on third-party vendors. This in-house capability substantially reduces lead times and lowers overall costs.
Progressive stamping also demands advanced expertise in computer numerical control (CNC) technology, as CNC systems automate the production of dies and control the stamping presses and coil feeders. Ajax maintains a team of highly skilled CNC machinists—among the finest in the metal forming industry—and continually invests in state-of-the-art facilities to ensure our in-house tooling capability delivers the excellent results our customers demand.
What Materials Are Used in Progressive Metal Stamping?
Selecting the right material, balancing performance and production efficiency, is crucial in progressive stamping. At Ajax, our sales engineers possess significant training and experience, holding Class A journeyman credentials to expertly match material properties with specific applications.
Commonly used metals in progressive stamping at Ajax include:
- Aluminum: Lightweight, corrosion-resistant, and highly formable, offering excellent thermal and electrical conductivity. Ideal for marine applications, exterior construction components, and device enclosures.
- Carbon Steel: Economical, strong, versatile, and highly formable. Typically used in hinges, fasteners, clips, and brackets.
- Stainless Steel: Renowned for superior corrosion resistance, durability, and strength. Commonly employed in medical instruments, food-grade equipment, and electronic components.
- Galvanized Steel: Zinc-coated carbon steel offering economical corrosion resistance. Frequently used for building components, brackets, and outdoor hardware.
- High-Strength Low-Alloy (HSLA) Steel: Known for exceptional yield strength, formability, durability, and weldability. Ideal for structural members, construction elements, and safety-critical automotive components.
- Copper: Offers outstanding electrical and thermal conductivity, ease of forming, and corrosion resistance. Commonly used in heat exchangers, circuit board components, and electrical connectors.
Material selection significantly impacts tooling requirements, production speeds, final product quality, and overall project cost.
What Finishing Processes Does Ajax Provide?
Ajax enhances stamped parts through various metal finishing services, including powder coating, anodizing, electro-polishing, and plating. Additionally, Ajax offers comprehensive product assembly using specialized fastening hardware and robotic welding. Ajax also provides kitting services, enabling efficient and economical downstream assembly.
How Does Ajax Provide Quality Assurance?
Quality assurance is integral to Ajax’s stamping operations, ensuring every part meets stringent standards. Ajax employs comprehensive inspection methods—from precision hand-held measurements using digital micrometers and calipers to advanced laser scanning technologies. These practices ensure dimensional accuracy, surface integrity, and material consistency, safeguarding against defects and reinforcing Ajax’s reputation for quality and compliance.
Progressive metal stamping operations incorporate rigorous quality controls, utilizing techniques like laser measurement, visual inspection, and in-line sensor technologies. These systems swiftly identify and correct anomalies, ensuring consistent product excellence.
Ajax also prioritizes environmental sustainability, actively reducing scrap, recycling metal waste, and optimizing energy efficiency throughout the stamping process. By designing processes and dies that minimize waste and implementing comprehensive recycling programs, Ajax contributes to sustainability efforts and achieves valuable cost savings.