Deep Drawn & Servo Stamping
Rely On Ajax Servo Presses For Speed & Precision
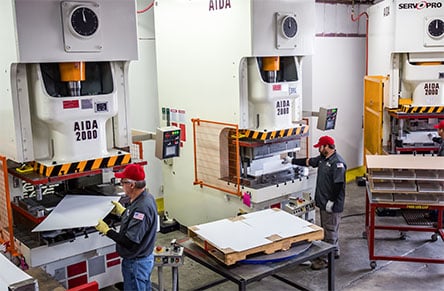
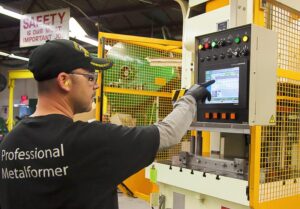
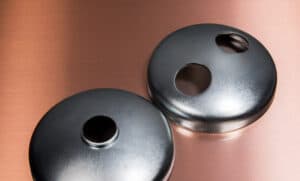
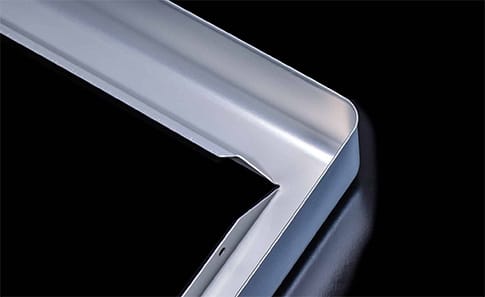
Deep Drawn & Servo Stamping Technology.
Ajax servo presses use advanced servo-motor technology and closed-loop control for precise motion, position, speed, and force control throughout the stroke. This enables highly accurate and repeatable results ideal for complex parts with tight tolerances.
These presses allow programmable stroke length, slide velocity, and force profiles within a cycle. This flexibility handles a wide variety of parts, dies, and speeds on the same machine. Different motion profiles are easily programmed, making servo presses ideal for tasks like deep drawing.
Although very precise, servo presses can operate at high speeds comparable to mechanical presses and faster than hydraulic ones. They achieve full working energy and tonnage at any speed for efficient high-speed production. Their electric operation is also more energy-efficient.
Contact an Ajax sales engineer today and find out more about deep drawn servo stamping solutions.
Deep Drawn & Servo Stamping FAQs
Why Choose Deep Drawn Stamping?
Once the necessary tooling is developed, deep drawn stamping provides efficient, repeatable part production that is highly cost-effective for large quantities of parts. Deep drawn is ideal for pans, cans, housings, enclosures, and other hollow parts without resorting to welding or seams. This saves additional production steps and reduces costs.
Deep drawing achieves consistent wall thickness, precise dimensions, and tight tolerances—crucial for parts where fit and finish are critical. Because the process yields smooth, seamless surfaces, deep drawn parts are well-suited for visible or cosmetic applications.
Why Choose Servo Stamping?
Servo presses use electric actuators rather than traditional mechanical flywheels or hydraulic systems. The movement of the ram is controlled with precision, constantly adjusting the slide’s speed, location, and dwell at any point in the press stroke. This fine-tuned control enables the use of a wider range of materials and part geometries while still achieving efficient production. Because servo presses can slow down the ram during critical forming points (like bottom dead center), they reduce material stress and allow for greater formability, ideal for high-strength steels, aluminum, and deep drawn parts. The result is less springback, wrinkling, and cracking.
What Materials Are Used?
Selecting the right material, balancing performance and production efficiency, is crucial in progressive stamping. At Ajax, our sales engineers possess significant training and experience, holding Class A journeyman credentials to expertly match material properties with specific applications.
Commonly used metals in progressive stamping at Ajax include:
- Aluminum: Lightweight, corrosion-resistant, and highly formable, offering excellent thermal and electrical conductivity. Ideal for marine applications, exterior construction components, and device enclosures.
- Carbon Steel: Economical, strong, versatile, and highly formable. Typically used in hinges, fasteners, clips, and brackets.
- Stainless Steel: Renowned for superior corrosion resistance, durability, and strength. Commonly employed in medical instruments, food-grade equipment, and electronic components.
- Galvanized Steel: Zinc-coated carbon steel offering economical corrosion resistance. Frequently used for building components, brackets, and outdoor hardware.
- High-Strength Low-Alloy (HSLA) Steel: Known for exceptional yield strength, formability, durability, and weldability. Ideal for structural members, construction elements, and safety-critical automotive components.
- Copper: Offers outstanding electrical and thermal conductivity, ease of forming, and corrosion resistance. Commonly used in heat exchangers, circuit board components, and electrical connectors.
Material selection significantly impacts tooling requirements, production speeds, final product quality, and overall project cost.
What Related Processes Does Ajax Provide?
Ajax enhances stamped parts through various metal finishing services, including powder coating, anodizing, electro-polishing, and plating. Additionally, Ajax offers comprehensive product assembly using specialized fastening hardware and robotic welding. Ajax also provides kitting services, enabling efficient and economical downstream assembly.
How Does Ajax Provide Quality Assurance?
Quality assurance is integral to Ajax’s stamping operations, ensuring every part meets stringent standards. Ajax employs comprehensive inspection methods—from precision hand-held measurements using digital micrometers and calipers to advanced laser scanning technologies. These practices ensure dimensional accuracy, surface integrity, and material consistency, safeguarding against defects and reinforcing Ajax’s reputation for quality and compliance.
Progressive metal stamping operations incorporate rigorous quality controls, utilizing techniques like laser measurement, visual inspection, and in-line sensor technologies. These systems swiftly identify and correct anomalies, ensuring consistent product excellence.
Ajax also prioritizes environmental sustainability, actively reducing scrap, recycling metal waste, and optimizing energy efficiency throughout the stamping process. By designing processes and dies that minimize waste and implementing comprehensive recycling programs, Ajax contributes to sustainability efforts and achieves valuable cost savings.